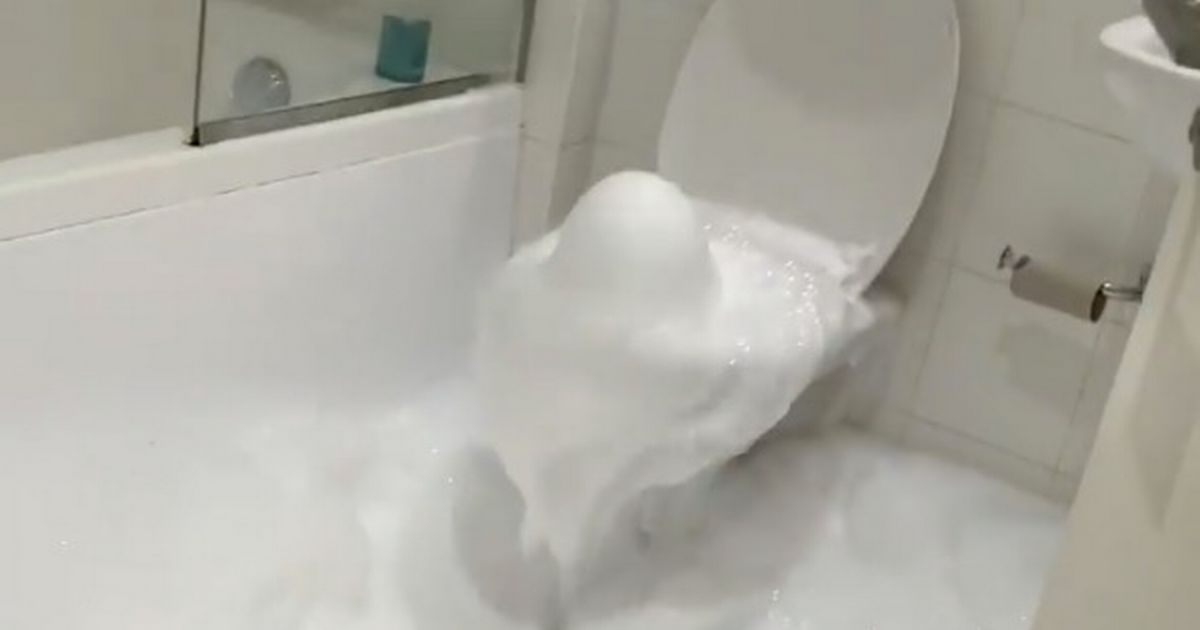
Want to install a washing machine? It might not be so easy.
Rick Hahn a Project Manager with our MEP Team explains.
The installation of in-unit washing machines and dryers is a popular renovation request that has become very popular in recent years particularly due to social distancing concerns with common laundry facilities. The added convenience of no longer having to carry load after load of laundry to the basement or an off-site laundromat is also huge time saver, but not every building will have the capabilities to allow for this amenity.
While limitations of the existing plumbing systems are a key factor in determining feasibility, more often the existing electrical service will be the primary obstacle. Most older buildings were not designed to account for an increase in electrical capacity at the apartment panels and/or the main electrical service. Added electrical load from new laundry equipment can exceed available electrical capacity supplied to the units or the building as a whole. Additionally, apartment panels may not have spaces to install the additional circuits required. An electrical load study will be required to determine the feasibility of adding these appliances.
The overall electrical requirements of the laundry equipment cold be reduced if a natural gas dryer can be installed, but that adds another set of hurdles. Even if there is existing natural gas riser that supplies gas to kitchen stoves or an in-unit furnace, new gas dryers could double the load on the gas riser. It’s unlikely the piping was sized to allow for this additional gas load, and without proper planning it could damage or render other connected appliances inoperable. A gas service inquiry with the utility company may be required to determine if adequate supply is available.
Regardless of the dryer’s heat source, most will require venting. Due to the high moisture content and lint accumulation in dryer exhaust, they must vent independently of all other gas appliances. This will require new exterior penetrations in addition to 3-4” vent piping routed through the unit, from the dryer to the building exterior. Building codes have strict requirements for limits to the length of vents, and space may not be available to maintain the necessary clearances from building openings like windows and terrace doors. Under no circumstances can these vents be connected to existing ventilation systems that serve common bathroom or kitchen groups. If the plumbing and electrical hurdles can be overcome, it may be likely that the only type of dryer that will be allowed is an electric condensing type dryer which would not require the vent connection to be brought to the outdoors.
After the power supply and venting are confirmed, the hot/cold water supply and sanitary drainage need to be considered. Washing machines require as much water as adding an additional shower. Supply piping may not be sized to accommodate this additional flow, which could lead to unintended water supply issues elsewhere in the building. Washing machines also have code specific drainage requirements to prevent the backup of suds into the plumbing systems of other dwelling units sharing drain lines. Reconfiguration of these concealed pipes may be required in order to prevent these types of backups from occurring, before installation can be approved.
All of these components should be considered when evaluating an alteration request, or considering a change to bylaws to allow individual installations. A feasibility assessment should be performed to get a assess the overall impact to common building systems, and identify any additional work in the building that might be required to allow an installation to move forward.